Gas Assisted Injection Moulding
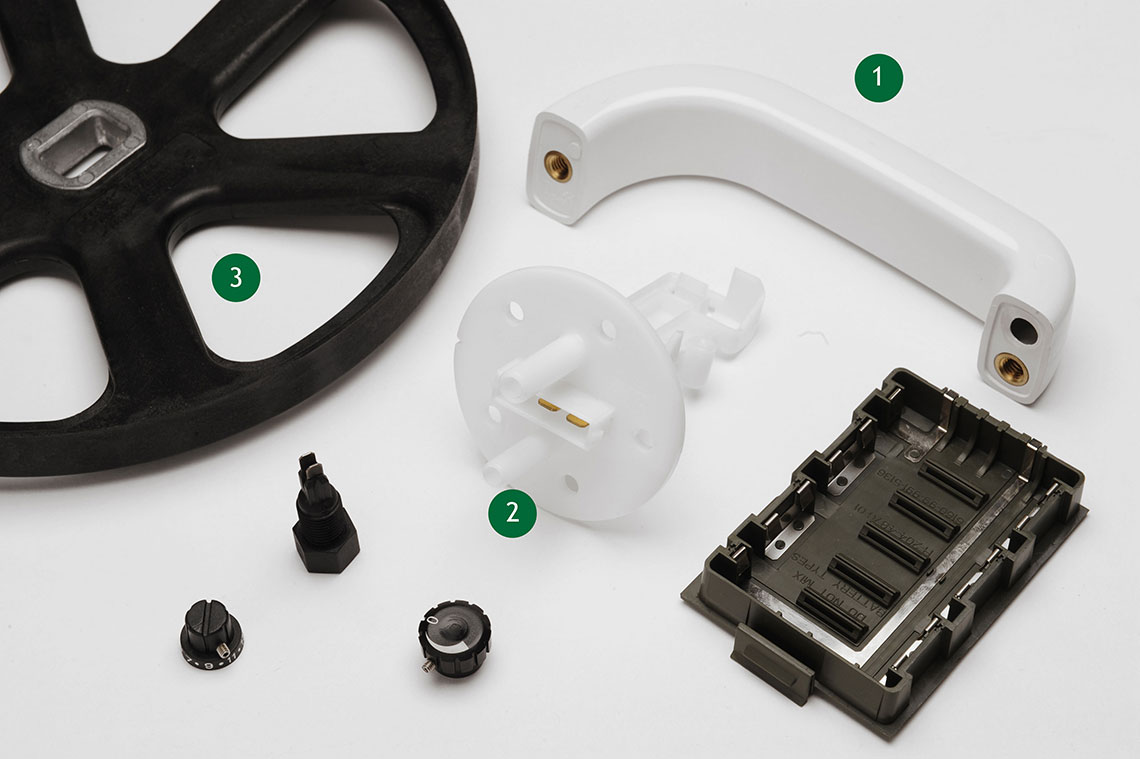
As leading injection moulding specialists, Fern Plastics provide gas-assisted injection moulding, also known as gas assist injection moulding, as an alternative to traditional plastic injection moulding. This variant of conventional injection moulding is a cost effective way to manufacture plastic parts when a cosmetic appeal is important.
What is Gas Assist Injection Moulding?
This type of injection moulding uses inert gases during the moulding process to produce plastic parts that are hollow and lightweight. After the plastic material is injected, the gas channels in the mould are filled with pressurised nitrogen gas. The gas’s high pressure maximises the flow of the resin and pushes the molten plastic into every extremity of the mould cavity. The high pressure is released when the plastic in the mould has cooled and hardened and the final product is hollow with a high-quality finish.
What are the Benefits of Using Gas Assisted Injection Molding?
The improved surface appearance of gas assist injection moulding products is one of the benefits of using this type of plastic injection moulding. Gas-assist injection moulding is very useful for the creation of hollow products that need to maintain structural integrity.
Key Benefits of using Gas Assist Injection Moulding
- Improves the overall quality of the end plastic product by eliminating cosmetic defects like irregularities on the surface and sink marks.
- Very cost-effective as less thermoplastic material is used in the process.
- Less energy is used during the manufacturing process which makes gas assist injection moulding more environmentally friendly than conventional injection moulding processes.
- During the gas injection moulding process, cooling time is shorter which lowers the overall cycle time.
- Dimensional stability is improved and the final product benefits from increased rigidity and strength.
- Smaller machines can be used for gas-assisted moulding because clamp force is reduced since the gas pressure is less than the pressure applied by the plastic during conventional injection moulding processes.
Applications for Gas-Assisted Moulding
Gas Assist injection molding is useful in the manufacturing of complex plastic parts that require a high level of aesthetic quality. The process yields a strong and rigid part and can produce large, thick and hollow sections to a high standard.
Popular Applications for Gas-Assisted Injection Molding
There are a number of common applications for gas assisted injection moulding, may of which are found in everyday household objects. Whilst you may already have any idea of how our gas-assist injection moulding services can help your project, here are just a few examples of common usage.
- Domestic appliance handles
- Furniture like countertops and tabletops
- Showerheads
- Computer and laptop enclosures
- Automotive panels
- Housing for medical equipment
What Are the Disadvantages of Gas Assist Injection Moulding?
At Fern Plastics, we don’t recommend the use of our gas-assist injection moulding service for polymers with high melt flow indexes. Lower viscosity resins displace too easily within the moulds and reduce the effectiveness of the process. This results in weaker sections and an overall inferior end product.
Fern Plastics has gained over 60 years of experience in providing injection moulding solutions in the West Midlands. If you would like to know more about our gas-assisted injection moulding services, contact us for more information or call us on 01902 758282