Ultrasonic Welding
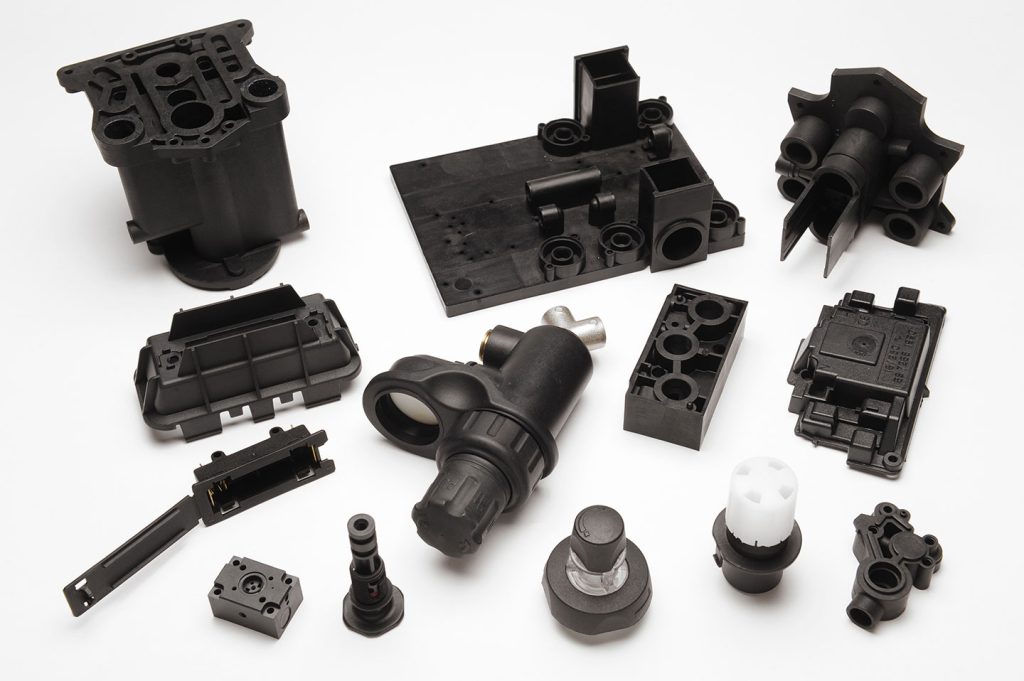
The range of value-added services we provide at Fern Plastics includes ultrasonic welding of plastic injection moulded parts. Sonic welding is a popular process that is used to neatly weld thermoplastic material without the use of heat or adhesives. As experts in plastic injection moulding, our ultrasonic welding services provide an economical solution for creating strong precision moulded products that are suitable for use in a wide variety of industries. Our team of engineers have years of experience in ultrasonic joining and each project is overseen by project managers and is subject to ultrasonic weld inspection to ensure you get the highest quality end result.
What is Ultrasonic Welding?
Ultrasonic plastic welding (also known as USW) is a widely used process that utilises ultrasonic vibrations and high pressure to weld thermoplastic materials together to form one assembled part. This process can weld similar and dissimilar plastic parts together without the need for external heat, fasteners or solvents.
During the sonic welding process, ultrasonic welding machines produce high-frequency sound waves or vibrations, typically at a frequency of 20 or 40 kHz. The plastic injection moulded parts to be welded are held together under pressure while ultrasonic welding takes place. High-frequency vibrations create intense heat energy that bonds plastic materials together at the contact point. Once cooled, the result is a strong assembled plastic product with a robust seamless join.
Ultrasonic seam welding is ideal for joining plastic injection moulded parts together and is a preferred assembly method across many industries including the medical and automotive industries. Many of our clients favour ultrasonic assembly since it offers a consistently repeatable performance that can be easily automated. This makes it highly suited to mass production. Additionally, this form of precision welding ensures that assembled plastic components form a tight seal, preventing the leakage of air or liquids in critical applications.
Ultrasonic seam joining is a suitable method for joining thermoplastics like Polypropylene PP, Polycarbonate PC and Acrylonitrile Butadiene Styrene ABS as well as joining metal and plastic parts together.
Benefits of Ultrasonic Welding
The varied benefits of ultrasonic welding make it a desirable value-added service for your plastic injection moulding requirements. Ultrasonic plastic welding is a cost-effective option for effectively joining your injection moulded parts since it eliminates the need for additional adhesives, solvents or mechanical fasteners. Clients who use our ultrasonic welding services also experience the benefit of faster assembly times thanks to the rapid cooling times of welded parts which can help to further reduce production costs.
Unlike other methods of welding, the process of ultrasonic joining allows greater flexibility in production because applications and tooling for assembly systems can be quickly exchanged for more versatility. The benefits of ultrasonic welding go on as this process produces a flawless strong seam which is virtually invisible making it ideal for products that demand a superior, visually appealing surface finish.
Ultrasonic welding also allows greater precision, ensuring that the assembled components achieve a pressure-tight fit, preventing leakage of water and gas. This level of accuracy is especially important for applications where airtight and watertight integrity is critical, such as in medical devices or automotive systems.
Key Advantages of Ultrasonic Welding:
- Exceptionally fast process
- Ideal for welding dissimilar materials
- Cost-effective
- Repeatable and easy to automate
- High-quality surface finish after welding
- Effectively welds very thin materials
- High-precision welding process which reduces the risk of heat damage to the product or surrounding surfaces.
- Ensures pressure-tight fit between welded components
- Less opportunity for human error with options for full automation
Key Applications for Ultrasonic Welding
The ultrasonic welding process is popular in many industries due to it being a rapid process that delivers clean, efficient results. For industries requiring pressure-tight plastic parts, ultrasonic welding provides seamless joins that maintain their integrity under air or liquid pressure. From delicate electrical circuits to car door panels and engine components, the applications for ultrasonic welding are seemingly endless. The accuracy and quality of sonic welding combined with the use of indirect heat, make it suitable for manufacturing parts within the aerospace industry. Medical equipment like face masks and gas filters benefit from the flawless surface finish and high-quality, tight seal that ultrasonic plastic welding can produce.
Key Uses for Ultrasonic Welding
- Medical equipment and instruments
- Automotive parts
- Electrical and electronic components
- Communications
- Household appliances
- Packaging
- Toys
- Consumer products
Fern Plastics provides exceptional ultrasonic welding services to compliment any precision injection moulding projects. Over 60 years of experience has made us a leading plastic injection molding company in the West Midlands and experts in ultrasonic welding plastic materials.
If you’d like more information about ultrasonic plastic welding or any of our other value added services, contact us online or call our team on 01902 758282.