[smartslider3 slider=”2″]
Polycarbonate Injection Moulding (PC)
Polycarbonate (PC) is an engineering plastic that is naturally transparent and extremely strong. In its unprocessed form, this amorphous thermoplastic can transmit light like glass and is used in a wide range of industrial and medical applications. Polycarbonate is either made of BPA (bisphenol A) and phosgene or BPA and diphenol carbonate. PC liquifies instead of burning which makes it very easy to mould and can be formed at room temperature without cracking or breaking. Polycarbonate injection moulding is used to create robust materials that are transparent and impact resistant.
This page is for informational purposes only. Fern Plastics provides injection moulding services and does not supply the material.
Properties of Polycarbonate (PC)
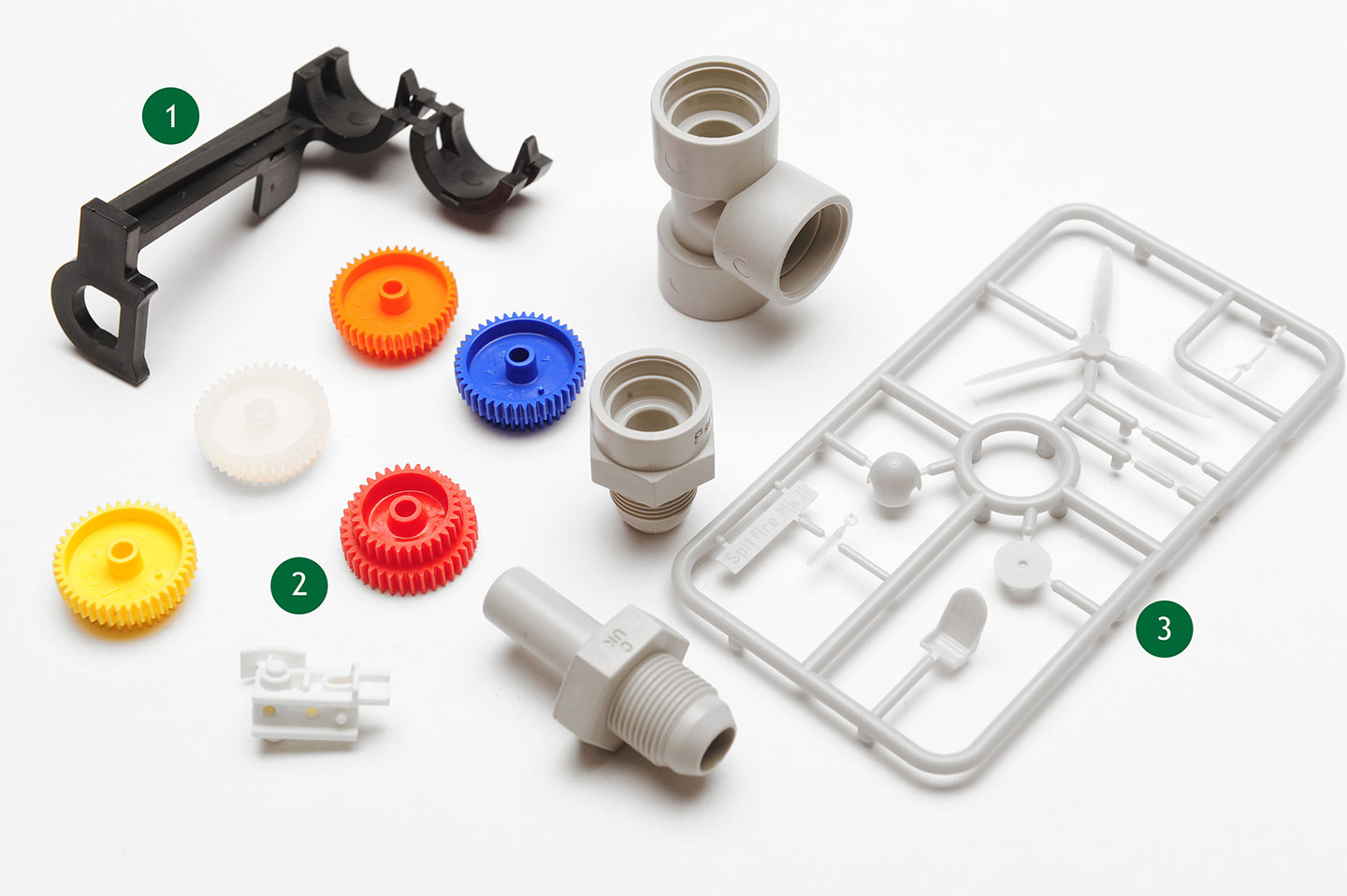
As well as being a high-performance engineering material, PC is very versatile and is commercially available in a variety of colours and grades of pigmentation. Polycarbonate is highly compatible with other engineering polymers and is most commonly combined with ABS ( Acrylonitrile Butadiene Styrene) to create PC/ABS.
- Excellent heat resistance
- High impact resistance
- Glass-like transparency
- UV resistant
- Lightweight
- Can be combined with other materials without degradation
Benefits of Using Polycarbonate Material in Plastic Injection Moulding
Using polycarbonate material for your plastic injection moulding projects comes with a wealth of benefits. The end product has superior impact resistance, chemical resistance and rigidity making it useful for a large range of applications and industries.
- Good thermal insulation
- Easy to cut and mould
- 250 times stronger than glass
- Low moisture absorption
- Excellent light transmission
- Recyclable
- Good electrical properties
- Polycarbonate products have a very smooth, flawless surface and are seamless
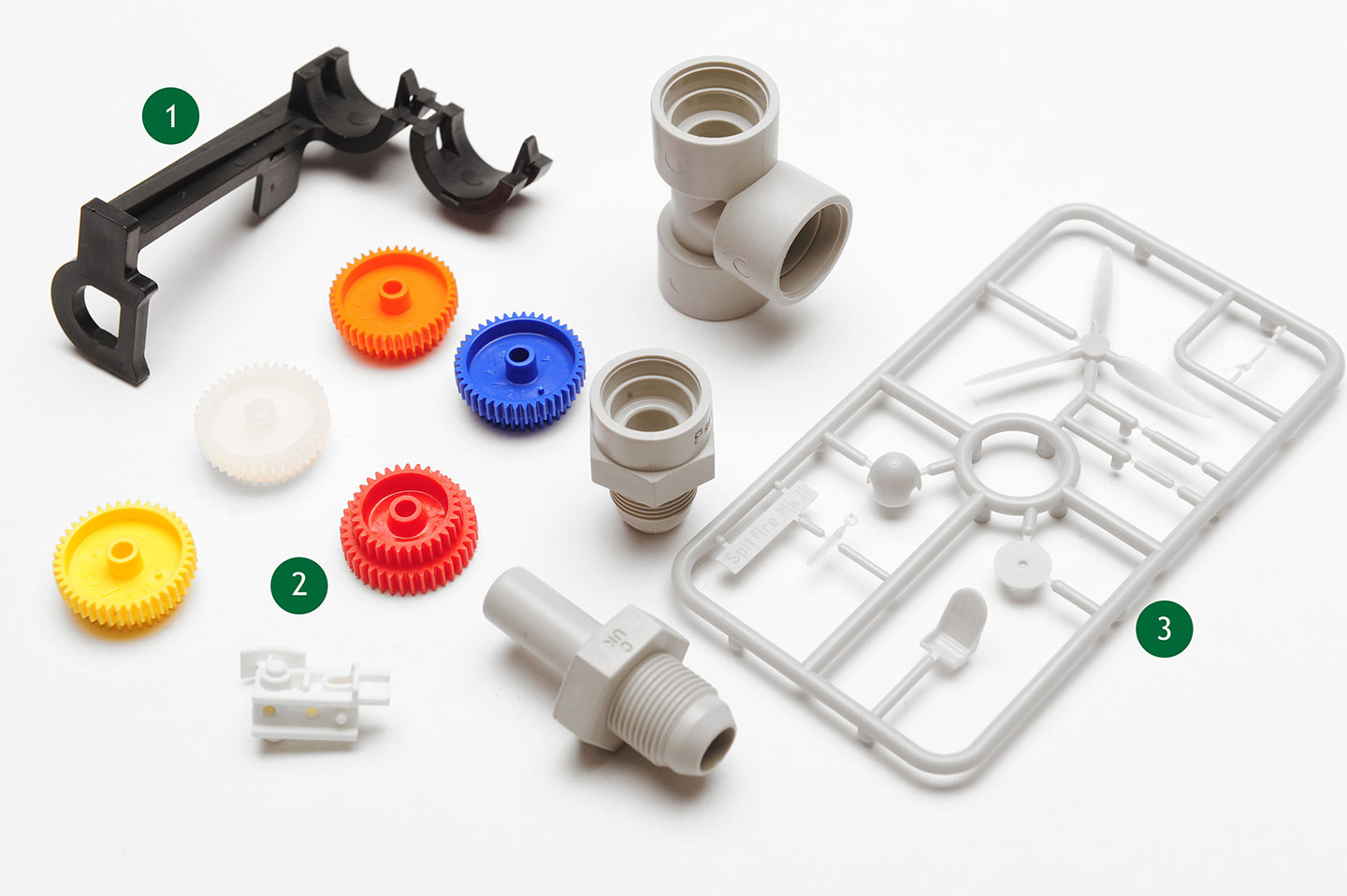
Common Polycarbonate Uses
PC material is used in plastic injection moulding processes to create products that require impact resistance or transparent qualities. The recyclability and eco-friendly processing quality of polycarbonate material make it suitable for use in medical equipment manufacturing, automotive industries as well as glazing and lighting manufacturing.
- Greenhouses
- Optical lenses
- Digital disks (CD’s, DVD, Blu-ray)
- Medical devices
- Aircraft parts
- Equipment housings
- Lighting fixtures
- Protective gear (face shields and protective eyewear)
- Telecommunications
Polycarbonate Disadvantages
There are many advantages to using PC for your injection moulding projects, however there are some disadvantages of using polycarbonate that may affect the plastic injection molding process.
- More expensive than glass or other plastics
- Low scratch resistance
- Low resistance to organic solvents
- Overexposure to sunlight can cause PC to turn yellow if additives are not used to prevent this
Using Polycarbonate Materials for Your Plastic Injection Moulded Project
The durability and strength of injection moulding polycarbonate make this thermoplastic the ideal choice for a wide range of industries and applications. Fern Plastics are specialists in plastic injection moulding with PC materials and we create high-quality injection moulding products using our readily available stock.
For more information on our injection moulding processes, contact us online today or call a member of our team on 01902 758282.
Polycarbonate FAQs
Can Polycarbonate be recycled, and how is it typically recycled?
Polycarbonate (PC) is recyclable, and it can be processed through various recycling methods to create new products. PC can be mechanically recycled where the material is shredded into pellets, melted and remoulded. This plastic can also be chemically recycled where it is turned into a molten material and reused. This process can potentially yield higher-quality material and reduce the degradation associated with mechanical recycling, although it is more complex and typically requires a higher investment.
What are the limitations of Polycarbonate in injection moulding?
As well as being prone to yellowing over time, polycarbonate can be prone to stress cracking and has limited chemical resistance. Polycarbonate PC surfaces can be prone to scratching, which may require additional protective coatings or surface treatments in applications where appearance and optical clarity are important.